The dredging and energy industries have significant roles in building a more sustainable world, and Royal IHC is providing the innovations in technology, procedures and processes to fuel this effort. In operation since 1642, the Dutch marine equipment and technology firm is now using data and machine learning to create digital twins of its vessels to proactively identify and mitigate mechanical issues that can cost its customers significant wasted time and money. With over 1,000 ships equipped with IoT sensors that generate billions of data points daily, Royal IHC faced scalability, performance and data governance limitations under its legacy system. Databricks Data Intelligence Platform helped provide a scalable architecture that unifies all its sensor data with AI to quickly identify parts maintenance issues, which lessens the impact for customers. Through machine learning, Royal IHC now helps vessel operators limit downtime of critical components, leading to more efficient operation and furthering their sustainability goals.
Struggling to operationalize billions of IoT data points per day
Dredging involves removing various materials from the bottom of large bodies of water, either to protect waterways, such as channels and harbors, to mine valuable resources, such as sand and minerals, or to clean up contamination from heavy metals. Conscious of the environment, Royal IHC understands the environmental impact that dredging has and actively improves the efficiency of its vessels. Major losses in efficiency occur when parts break down in these intricate and complex vessels, which, given the abrasive nature of dredging, is common and can quickly lead to crucial problems. Therefore, Royal IHC and its customers need to know when small things are breaking to prevent significant problems down the line.
"It's all about detecting equipment failure so that our clients can operate efficiently," says Bram Visser, Data Scientist at Royal IHC. "By building digital twins, we aim to create a digital version of a vessel that learns standard operational behaviors and can then identify anomalies to determine when there is an issue so we can immediately intervene."
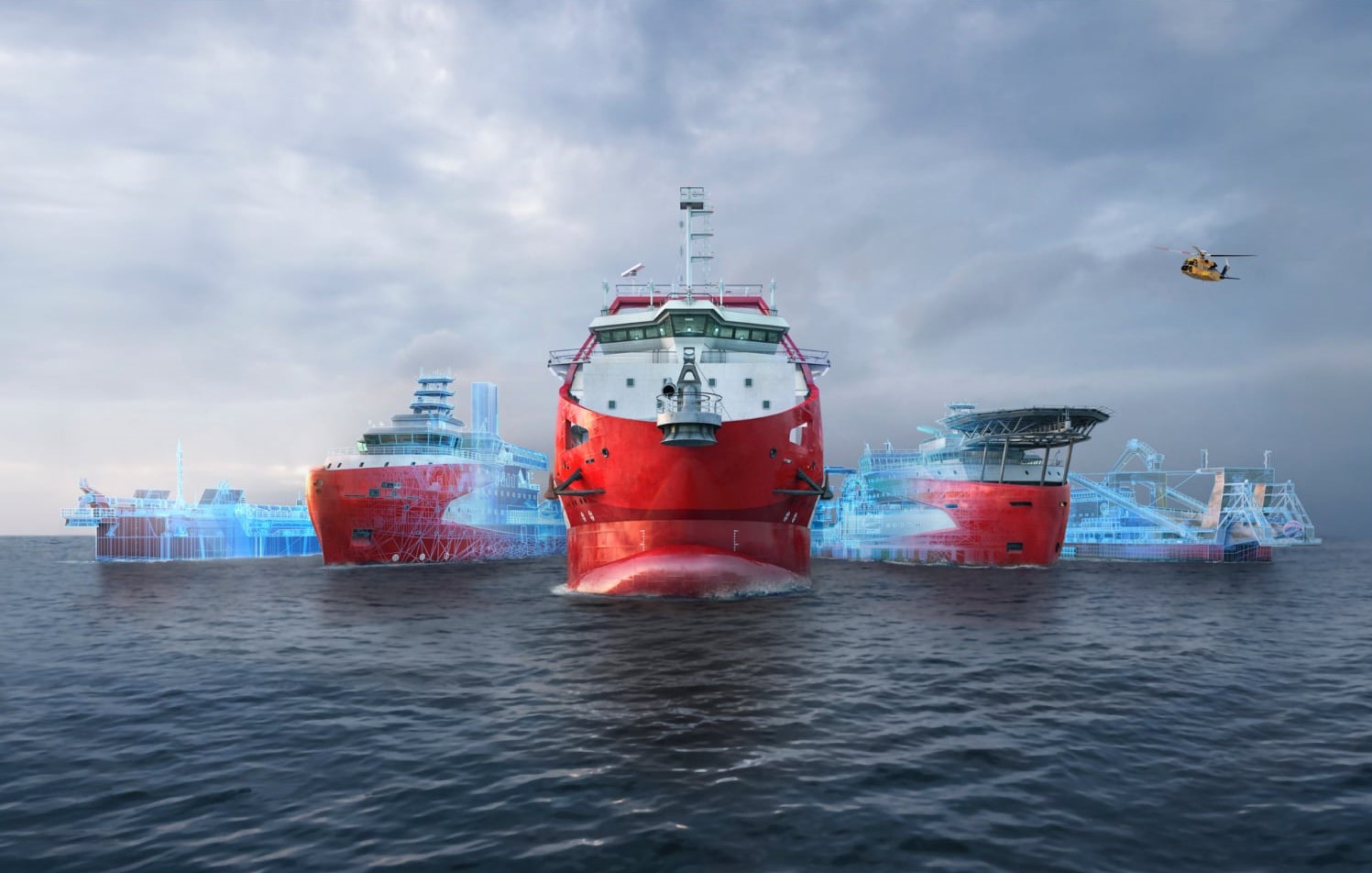
With the number of components on vessels and thousands of IoT sensors generating thousands of data signals per vessel, Royal IHC's Azure database proved unable to keep up with the level of data being generated. In addition, performance issues and limited technical tools for collaboration were a constant challenge, as its data scientists were forced to work on individual laptops to explore their data and train their predictive models.
To realize its vision for digitally powered predictive maintenance, Royal IHC needed a cost-effective solution that could scale its models and empower clients to operate more efficiently – that's where Databricks came in.
Scalable analytics and better ML for predicting outcomes
Understanding the need for a revamped architecture that could meet its data, analytics and AI requirements, Royal IHC chose Databricks Data Intelligence Platform for its ability to handle data ingestion at scale, efficiently manage the machine learning lifecycle and facilitate better cross-team collaboration. Databricks provides a centralized platform for data engineering to the production of machine learning models that deliver the insights they need to develop innovations fast. Delta Lake provides the foundational layer to store all the data generated by thousands of vessels and simplifies the building of reliable and fast data pipelines for analysts and data scientists alike.
Through seamless integration of Databricks Data Intelligence Platform with Grafana, analysts can create external visualizations for customers onshore to better observe and understand how their vessels perform in near real-time. And Royal IHC's team of data scientists use MLflow for model training and versioning, allowing them to fine-tune their ability to predict equipment failures accurately.
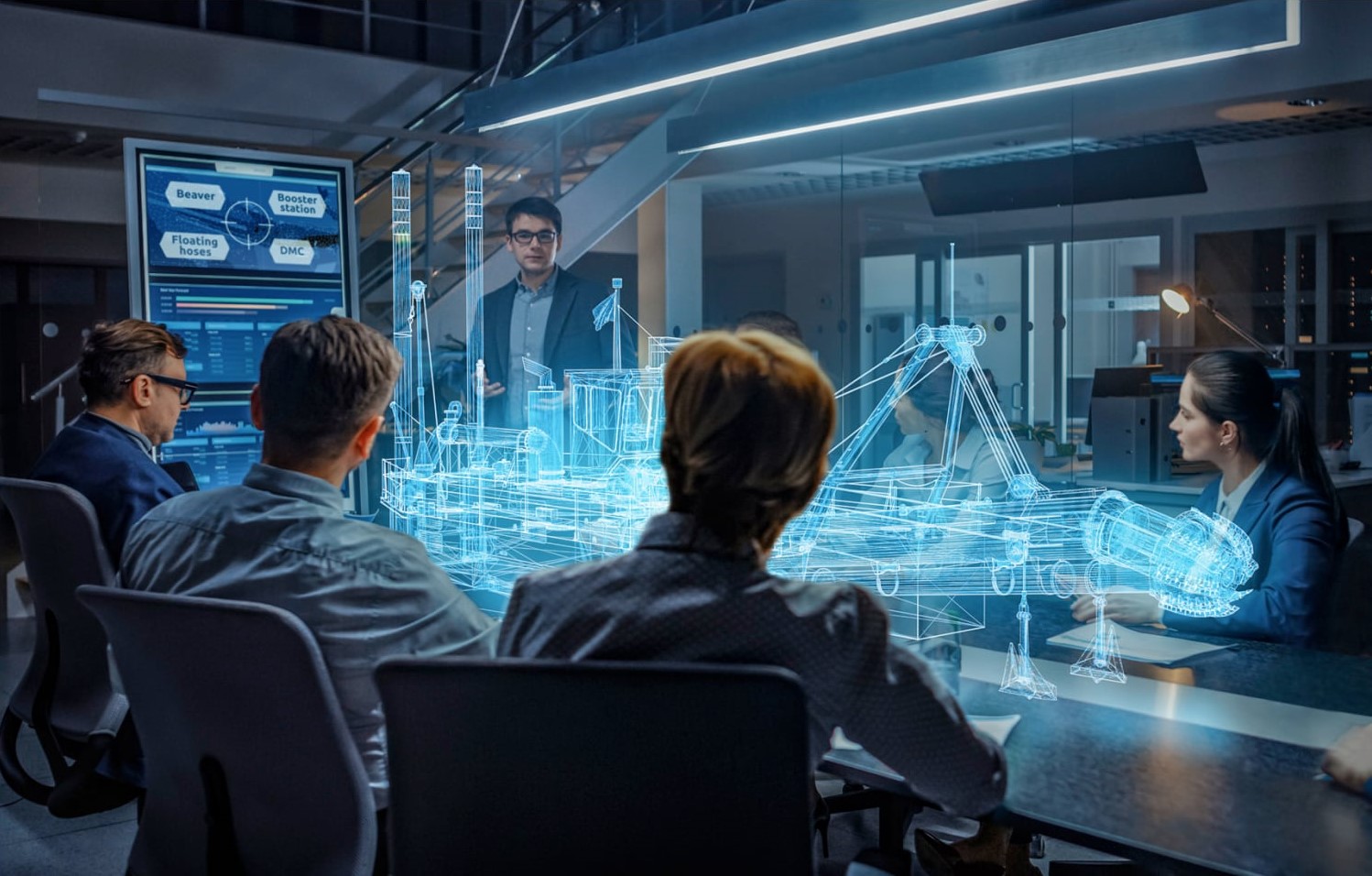
"Databricks has dramatically simplified the way we work with our data. We are no longer limited by resource or technology constraints," explained Visser. "Across our extended data team, from the engineers to analysts to data scientists, we have the tools necessary to operationalize our data in previously impossible ways."
Soon, Royal IHC will expand its use of Databricks Data Intelligence Platform to help internal business teams take a more data-first approach to decision-making. With Databricks SQL, they'll be able to democratize data insights through self-service tools and enhanced visualization for teams from finance to customer service.
Propelling dredging more sustainably
Fueled by Databricks, Royal IHC is harnessing the power of its data for better decision-making and machine learning innovations designed to improve vessel operations and customer satisfaction. The lakehouse architecture has unblocked previous performance and scalability issues, accelerating the company's ability to explore data and train models by 15x.
"It used to take us a full month to train 30 models. Now it takes only two days," said Visser. "This shorter time-to-market directly benefits our customers, as they can operate their vessels more cost-effectively."
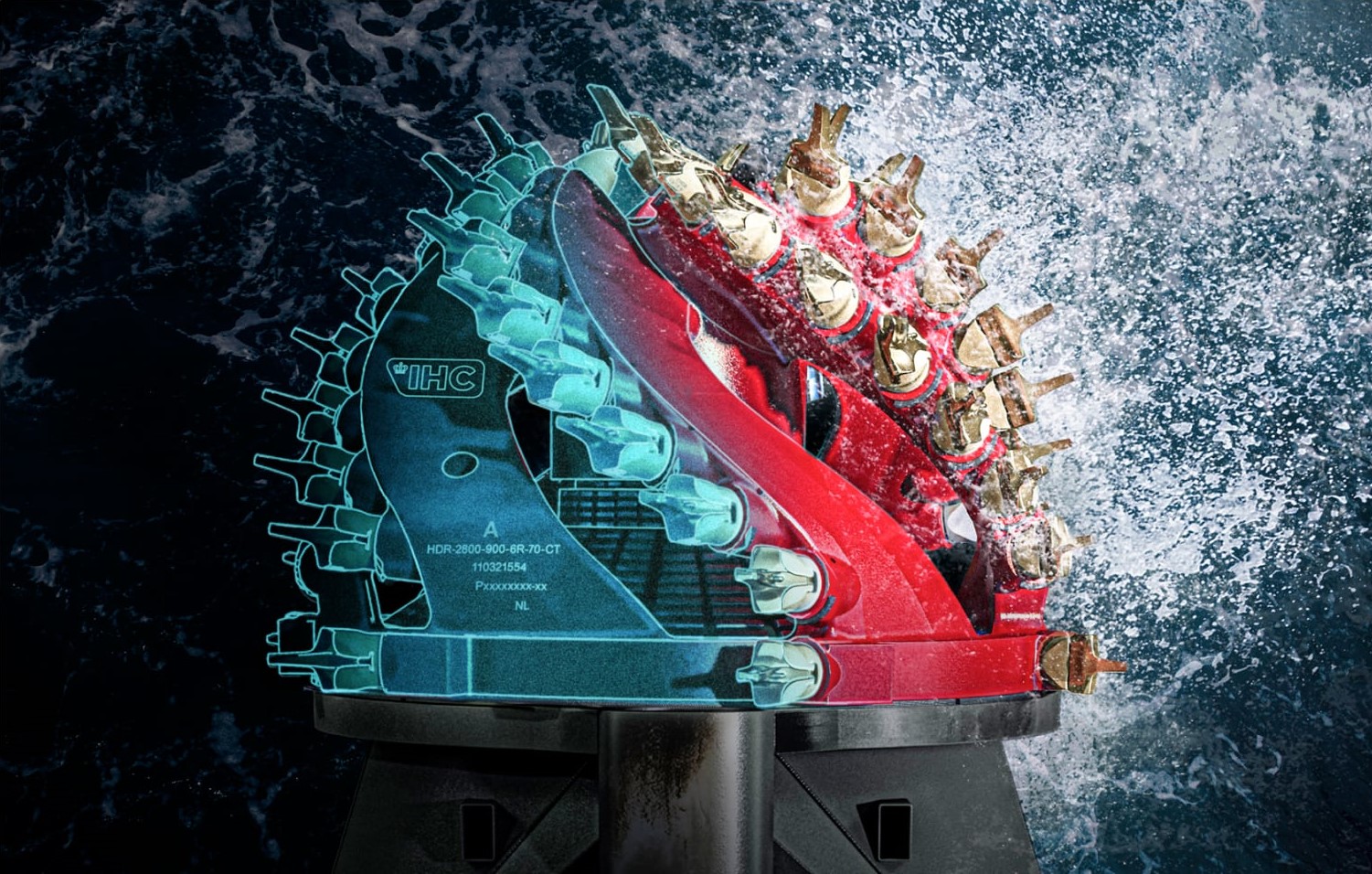
This speedup has allowed Royal IHC to create and deploy hundreds of models in production, resulting in an estimated maintenance cost reduction of 9%, downtime and service time reduction of 45%, and increased overall customer satisfaction.
Looking ahead, Royal IHC plans to dive deeper into machine learning to better understand and mitigate abnormal operating behavior, as well as analyze ERP data to classify vessel parts that will save hundreds of workforce hours and improve supply chain efficiency. With the lakehouse, Royal IHC will further establish a data-driven culture, supporting its quest to dredge more sustainably.